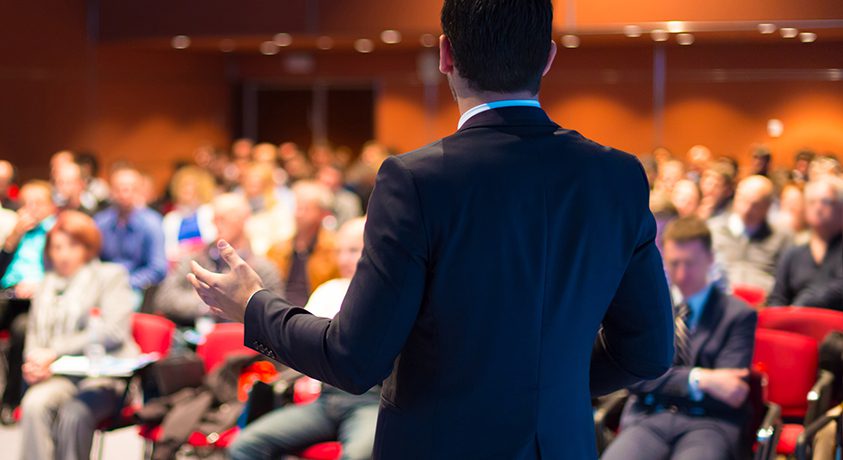
Editor’s Note: This article was originally published in the March issue of BONEZONE®. We’re sharing it here to bring greater awareness to the regulatory challenges faced by the orthopedic industry and our collaboration with OSMA.
The Orthopaedic Surgical Manufacturers Association (OSMA) is on a mission to expand its reach and influence in the device development process.
“Over the past 12 months, we’ve taken steps to identify and engage with diverse partners,” said Ehab Esmail, President of OSMA and Senior Vice President of Global Quality, Regulatory and Clinical Affairs at Orthofix. “We’re currently updating our bylaws to welcome new members who represent various facets of the industry. We’re also exploring collaborations with other organizations, such as ORTHOWORLD®, which share a focus on the orthopedic industry.”
OSMA was founded 70 years ago to align the orthopedic industry’s standards, communicate with regulators and develop new strategies. There’s been a significant shift in the industry’s landscape since then.
“Many of the manufacturers now rely on sophisticated suppliers to bring devices to market,” Esmail said. “In the past, suppliers were primarily machine shops depending on manufacturers for quality control. The landscape has changed. Suppliers have evolved in terms of regulations, testing and quality management systems.”
Recognizing this transformation, Esmail believes OSMA must become more inclusive to involve all stakeholders in the orthopedic industry, including suppliers in the supply chain, testing labs, consultants and legal professionals contributing to regulatory compliance.
Currently, orthopedic manufacturers find themselves navigating different sets of requirements, such as European and FDA regulations.
“Our goal is to drive initiatives that bring alignment to the industry and create universal standards for quality and testing,” Esmail said. “We believe that products intended for the same patient population should adhere to a single set of requirements to ensure safety and effectiveness. Our focus is on assessing and mitigating risks uniformly, regardless of the specific regulatory pathway taken to bring a product to market.”
At OMTEC 2024, OSMA will run education sessions on biocompatibility requirements, EU MDR regulations, international market forces and best practices in audit preparation. Esmail recently discussed why he’s excited about the opportunity to collaborate in person with the orthopedic professionals who will help grow OSMA’s influence throughout the industry.
Why is it important for OSMA to be an active participant at OMTEC as you begin a collaborative partnership with ORTHOWORLD?
Esmail: There’s significant synergy and overlap between OSMA and OMTEC. When we as manufacturers address our suppliers, the focus is on how their actions impact our operations. While they excel in manufacturing products and technologies, we need to ensure accountability for changes that may affect our registration processes.
We want to delve into the synergies between manufacturers and suppliers. What changes can suppliers make without notifying manufacturers? What changes could impact MDR or biocompatibility requirements? What changes get audited as a critical supplier? It’s important to look at how suppliers and manufacturers interact and ways to best navigate the intricacies of these relationships.
Understanding the intricacies of the manufacturer/supplier relationship is crucial for manufacturers because disruptions in the registration process could impede their ability to supply products for an extended period. Suppliers would also benefit from carving out the specific types of changes that could affect their relationships with manufacturers and understanding the product and regulatory environment within the high-level areas where we see that alignment is needed: EU MDR, biocompatibility, critical suppliers and change management.
OSMA is planning to discuss the complexities of biocompatibility requirements at OMTEC. Why is this an important topic?
Esmail: FDA is undergoing a transformation that’s like what occurred in the EU, which shifted its focus to evaluate the factors that influence biocompatibility. This involves not only ensuring that raw materials are biocompatible, but also examining the additives introduced during the manufacturing process. The emphasis extends to the cleanability of the final product and understanding how specific additives affect biocompatibility.
FDA’s increased focus on biocompatibility raises crucial questions from the industry perspective. Manufacturers rely heavily on testing labs to guide them on necessary tests and reports. However, there’s a disconnect when biocompatibility reports submitted to FDA prompt numerous questions. This situation puts manufacturers and suppliers in the difficult position of performing biocompatibility activities, but ending up with a report that’s not representative of FDA’s expectations.
We want to bridge the gap between expert recommendations and FDA expectations. The objective is to perform the same biocompatibility tests for European and U.S. markets and submit identical reports without encountering substantial pushback or questions regarding the testing procedures. Additionally, there’s a need to establish effective change management protocols to determine when new biocompatibility tests are required and how to navigate the impacts of such changes.
You want to touch on best practices in running successful audits. What will that involve?
Esmail: Certainly, each auditor has a distinct area of focus based on their expertise and background. Auditors tend to dig deep into their specific domains because they don’t want to work outside of their comfort zones, which shapes the nuances of each audit. However, there are common hot topics that most auditors frequently address, such as the management of CAPAs and change management.
There are also new MDR audit requirements that manufacturers need to fully understand. To enhance that understanding at OMTEC, it would be valuable to have a notified body auditor share insights into MDR-specific areas and outline the disparities between MDD and MDR audits.
Additionally, FDA is evolving its recognition of ISO 13485, but is also incorporating additional requirements. We want to shed light on this development with a discussion about FDA’s perspective. This is particularly crucial moving forward because FDA will acknowledge notified body audits, but this recognition will introduce unique aspects, similar to the distinctions observed in MDSAP.
Considering the complexity introduced by FDA’s additional requirements based on ISO 13485, addressing the perspectives of manufacturers and suppliers would benefit attendees. The insights shared will prepare them for these evolving audits, ensuring that manufacturers and suppliers are well-equipped to navigate the intricacies of compliance.
How is the international market evolving, and how do the regulations impact device design and development?
Esmail: They’re aligning more with MDR requirements. At the same time, FDA is aligning with the MDR Quality Management System, indicating a global movement toward harmonizing certain standards. While the world market is gradually converging on specific requirements, a significant challenge lies in the unique nuances or variations that each country introduces, particularly in areas like MR testing and safety labeling. Can we align these types of differences as an industry to ensure there aren’t distinct labeling requirements for markets in Europe, the U.S. and Canada? Achieving this alignment is imperative for our healthcare customers, who follow and interpret labels consistently.
Orthopedic professionals have discussed and dissected MDR regulations for years. How will OSMA approach this topic in a new way?
Esmail: The significant challenge ahead lies is effectively managing changes to a product’s design after MDR approval. Manufacturers and suppliers must understand the level of permissible changes and whether changes can be made during the review process. The timing of these changes is another factor to consider.
Understanding the impact and limitations of MDR approval is essential. Can suppliers alter manufacturing processes or specific elements? What types of changes are critical enough to trigger a new MDR review and what are the costs associated with that additional review? The expense and time involved may be a limiting factor for making beneficial changes to a product’s design.
Grasping the implications of changes following MDR approval ensures that stakeholders involved in the device development process are well-prepared. Manufacturers and suppliers can make informed decisions when they know how changes under MDR affect the manufacturing process.
Editor’s Note: This article was originally published in the March issue of BONEZONE®. We’re sharing it here to bring greater awareness to the regulatory challenges faced by the orthopedic industry and our collaboration with OSMA.
The Orthopaedic Surgical Manufacturers Association (OSMA) is on a mission to expand its reach and influence...
Editor’s Note: This article was originally published in the March issue of BONEZONE®. We’re sharing it here to bring greater awareness to the regulatory challenges faced by the orthopedic industry and our collaboration with OSMA.
The Orthopaedic Surgical Manufacturers Association (OSMA) is on a mission to expand its reach and influence in the device development process.
“Over the past 12 months, we’ve taken steps to identify and engage with diverse partners,” said Ehab Esmail, President of OSMA and Senior Vice President of Global Quality, Regulatory and Clinical Affairs at Orthofix. “We’re currently updating our bylaws to welcome new members who represent various facets of the industry. We’re also exploring collaborations with other organizations, such as ORTHOWORLD®, which share a focus on the orthopedic industry.”
OSMA was founded 70 years ago to align the orthopedic industry’s standards, communicate with regulators and develop new strategies. There’s been a significant shift in the industry’s landscape since then.
“Many of the manufacturers now rely on sophisticated suppliers to bring devices to market,” Esmail said. “In the past, suppliers were primarily machine shops depending on manufacturers for quality control. The landscape has changed. Suppliers have evolved in terms of regulations, testing and quality management systems.”
Recognizing this transformation, Esmail believes OSMA must become more inclusive to involve all stakeholders in the orthopedic industry, including suppliers in the supply chain, testing labs, consultants and legal professionals contributing to regulatory compliance.
Currently, orthopedic manufacturers find themselves navigating different sets of requirements, such as European and FDA regulations.
“Our goal is to drive initiatives that bring alignment to the industry and create universal standards for quality and testing,” Esmail said. “We believe that products intended for the same patient population should adhere to a single set of requirements to ensure safety and effectiveness. Our focus is on assessing and mitigating risks uniformly, regardless of the specific regulatory pathway taken to bring a product to market.”
At OMTEC 2024, OSMA will run education sessions on biocompatibility requirements, EU MDR regulations, international market forces and best practices in audit preparation. Esmail recently discussed why he’s excited about the opportunity to collaborate in person with the orthopedic professionals who will help grow OSMA’s influence throughout the industry.
Why is it important for OSMA to be an active participant at OMTEC as you begin a collaborative partnership with ORTHOWORLD?
Esmail: There’s significant synergy and overlap between OSMA and OMTEC. When we as manufacturers address our suppliers, the focus is on how their actions impact our operations. While they excel in manufacturing products and technologies, we need to ensure accountability for changes that may affect our registration processes.
We want to delve into the synergies between manufacturers and suppliers. What changes can suppliers make without notifying manufacturers? What changes could impact MDR or biocompatibility requirements? What changes get audited as a critical supplier? It’s important to look at how suppliers and manufacturers interact and ways to best navigate the intricacies of these relationships.
Understanding the intricacies of the manufacturer/supplier relationship is crucial for manufacturers because disruptions in the registration process could impede their ability to supply products for an extended period. Suppliers would also benefit from carving out the specific types of changes that could affect their relationships with manufacturers and understanding the product and regulatory environment within the high-level areas where we see that alignment is needed: EU MDR, biocompatibility, critical suppliers and change management.
OSMA is planning to discuss the complexities of biocompatibility requirements at OMTEC. Why is this an important topic?
Esmail: FDA is undergoing a transformation that’s like what occurred in the EU, which shifted its focus to evaluate the factors that influence biocompatibility. This involves not only ensuring that raw materials are biocompatible, but also examining the additives introduced during the manufacturing process. The emphasis extends to the cleanability of the final product and understanding how specific additives affect biocompatibility.
FDA’s increased focus on biocompatibility raises crucial questions from the industry perspective. Manufacturers rely heavily on testing labs to guide them on necessary tests and reports. However, there’s a disconnect when biocompatibility reports submitted to FDA prompt numerous questions. This situation puts manufacturers and suppliers in the difficult position of performing biocompatibility activities, but ending up with a report that’s not representative of FDA’s expectations.
We want to bridge the gap between expert recommendations and FDA expectations. The objective is to perform the same biocompatibility tests for European and U.S. markets and submit identical reports without encountering substantial pushback or questions regarding the testing procedures. Additionally, there’s a need to establish effective change management protocols to determine when new biocompatibility tests are required and how to navigate the impacts of such changes.
You want to touch on best practices in running successful audits. What will that involve?
Esmail: Certainly, each auditor has a distinct area of focus based on their expertise and background. Auditors tend to dig deep into their specific domains because they don’t want to work outside of their comfort zones, which shapes the nuances of each audit. However, there are common hot topics that most auditors frequently address, such as the management of CAPAs and change management.
There are also new MDR audit requirements that manufacturers need to fully understand. To enhance that understanding at OMTEC, it would be valuable to have a notified body auditor share insights into MDR-specific areas and outline the disparities between MDD and MDR audits.
Additionally, FDA is evolving its recognition of ISO 13485, but is also incorporating additional requirements. We want to shed light on this development with a discussion about FDA’s perspective. This is particularly crucial moving forward because FDA will acknowledge notified body audits, but this recognition will introduce unique aspects, similar to the distinctions observed in MDSAP.
Considering the complexity introduced by FDA’s additional requirements based on ISO 13485, addressing the perspectives of manufacturers and suppliers would benefit attendees. The insights shared will prepare them for these evolving audits, ensuring that manufacturers and suppliers are well-equipped to navigate the intricacies of compliance.
How is the international market evolving, and how do the regulations impact device design and development?
Esmail: They’re aligning more with MDR requirements. At the same time, FDA is aligning with the MDR Quality Management System, indicating a global movement toward harmonizing certain standards. While the world market is gradually converging on specific requirements, a significant challenge lies in the unique nuances or variations that each country introduces, particularly in areas like MR testing and safety labeling. Can we align these types of differences as an industry to ensure there aren’t distinct labeling requirements for markets in Europe, the U.S. and Canada? Achieving this alignment is imperative for our healthcare customers, who follow and interpret labels consistently.
Orthopedic professionals have discussed and dissected MDR regulations for years. How will OSMA approach this topic in a new way?
Esmail: The significant challenge ahead lies is effectively managing changes to a product’s design after MDR approval. Manufacturers and suppliers must understand the level of permissible changes and whether changes can be made during the review process. The timing of these changes is another factor to consider.
Understanding the impact and limitations of MDR approval is essential. Can suppliers alter manufacturing processes or specific elements? What types of changes are critical enough to trigger a new MDR review and what are the costs associated with that additional review? The expense and time involved may be a limiting factor for making beneficial changes to a product’s design.
Grasping the implications of changes following MDR approval ensures that stakeholders involved in the device development process are well-prepared. Manufacturers and suppliers can make informed decisions when they know how changes under MDR affect the manufacturing process.
You are out of free articles for this month
Subscribe as a Guest for $0 and unlock a total of 5 articles per month.
You are out of five articles for this month
Subscribe as an Executive Member for access to unlimited articles, THE ORTHOPAEDIC INDUSTRY ANNUAL REPORT and more.
DC
Dan Cook is a senior editor with more than 18 years of experience in medical publishing and an extensive background in covering orthopedics and outpatient surgery. He joined ORTHOWORLD to develop content focused on important industry trends, top thought leaders and innovative technologies.