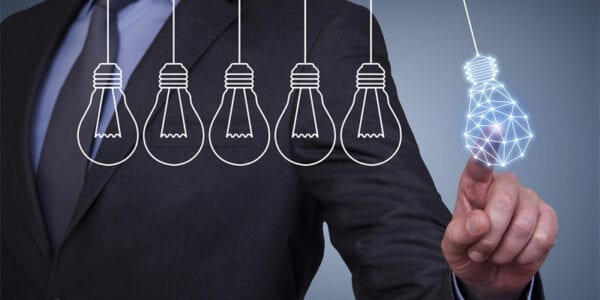
Earlier this year, a Member sent us a question: What portion of new products introduced in joint reconstruction and spine are additively manufactured?
This question had been on our radar for some time. Additive manufacturing (AM) has generated more interest than any other topic we’ve written about or presented at OMTEC in the last two years. Internally, we’ve wondered, is it just buzz or are companies actually adopting the technology? To investigate, we tracked products launches and regulatory announcements from January 2015 to 2017. Nearly two dozen companies were mentioned in ORTHOFLASH® during this time period. For your benefit, we’ve listed these companies, their market segments and products below. We’ve also included executive insight that we found to be valuable.
Our analysis leads us to state that >5% of joint reconstruction and spine products launched or about to be launched in the last two years incorporate additive manufacturing.
Work still needs to be done. This is not a comprehensive list of companies using the technology, nor does it represent all AM-related products on the market, but it is a start. We expect that more device and supplier companies will adopt additive manufacturing once more regulatory guidelines are established and patient outcome evidence is generated.
4WEB
Spine | Commenced U.S. launch of 3D-printed Posterior Spine Truss system of interbody fusion devices, with applications including PLIF, TLIF and Oblique procedures.
Amedica
Spine | Fabricated its first silicon nitride structures with a 3D printing process called robotic deposition, or robocasting. The products have been scanned with electron microscopy to confirm integrity and validity of the additive manufacturing method, and have demonstrated similar theoretical density and microstructure attributes to traditionally-manufactured silicon nitride fusion devices currently in use.
Beijing AK Medical
Joint | Received approval by the Chinese State FDA for the 3D ACT hip system, reportedly the first approval in China for an additively-manufactured orthopaedic implant.
ConforMIS
Joint | Commenced full commercial launch of the iTotal PS customized posterior stabilized total knee. The company’s knee implants and instrumentation are manufactured additively.
Joint | Introduced the next-gen iTotal CR (cruciate-retaining) total knee, designed to further reduce intraoperative steps during knee replacement.
EIT/Emerging Implant Technologies
Spine | Announced the first patient treated with an anatomically-adapted 3D printed titanium fusion implant, in a case of cervical spine degeneration.
Globus Medical
Spine | Investing in 3D printing equipment, but sees it as best applied to custom implants for scoliosis or anatomic abnormalities; not seeing benefit of 3D-printed implants for the vast majority of procedures, especially as many manufacturers utilize surface coatings that support bony ongrowth
HT Medical
Spine | Development pipeline includes products based on proprietary 3D-printed titanium additive technology from Additive Innovations
Johnson & Johnson
n/a | Sandi Peterson, Executive Vice President, Group Worldwide Chairman, explained how JNJ is an enterprise entity that can offer broad services to customers. This is the foundation for how they will win—using size and scale to serve hospitals and patients. Pieces of the strategy include use of technology to reduce development cycles, employ advanced analytics to get real-time views on data (which can be echoed company-wide), and harness capabilities like 3D printing. (They just announced a new partnership with HP.)
joimax
Spine | Launched the EndoLIF® On-Cage for spinal stabilization and fusion in the U.S. The 3D-printed titanium alloy EndoLIF On-Cage supports a mini-open or an inter-muscular approach.
K2M
Spine | Received FDA 510(k) clearances to market CASCADIA™ Cervical and CASCADIA AN Lordotic Oblique Interbody systems, featuring Lamellar 3D-printed Titanium Technology™.
Lima
Joint | Launched SMR® Stemless for its shoulder replacement portfolio, combining modularity and a proprietary Trabecular Titanium structure. Produced with additive manufacturing through electron beam melting, SMR Stemless features a 3D structure designed to imitate natural bone with clinically-proven osteointegration.
Medacta
Spine | Completed initial U.S. surgeries using its proprietary 3D-printed MySpine Patient Matched Technology Low Profile Guide, following FDA clearance.
Medicrea
Spine | Filed its FDA 510(k) submission for 3D-printed titanium interbody devices with compatible UNiD™ Lab surgical planning and analytical services.
Mighty Oak Medical
Spine | Received a second FDA 510(k) clearance for FIREFLY® Pedicle Screw Navigation Guides, extending compatibility to essentially all currently cleared pedicle screw systems and extending indications to include the T1-S2/ilium region. FIREFLY comprises patient-matched bone models and intra-op pedicle screw guides created via 3D printing.
NextStep Arthropedix
Joint | Received FDA 510(k) clearance for the iNSitu cementless total hip, additively manufactured via Electron Beam Melting; includes a highly cross-linked Vitamin E UHMWPE bearing
Nexxt Spine
Spine | Launched the DT Elite Guide System, intended to reduce the number of operative steps and simplify anterior cervical discectomy and fusion. DT Elite, manufactured through 3D printing technology, bridges a gap between the company’s Struxxure Anterior Cervical Plate and Honour Cervical Interbody systems.
Spine | Developing NanoMatrixx, 3D printed porous bioactive titanium material designed to actively participate in intervertebral fusion. NanoMatrixx’s micro and nanosurface topography with 70% porosity is intended to stimulate mesenchymal stem cells to differentiate into bone-forming osteoblasts.
Orthofix
Spine | Announced FDA 510(k) clearance and U.S. limited launch of the FORZA® PTC™ (PEEK Titanium Composite) Spacer. The system features PEEK and 3D-printed titanium endplates for use in lumbar spinal fusion to treat degenerative disc disease.
Oxford Performance Materials
Spine | Received FDA 510(k) clearance to market the SpineFab® VBR implant, reportedly the first FDA-cleared 3D-printed load-bearing polymer device for long-term implantation.
Renovis
Spine | Received FDA 510(k) clearance to market the Tesera™ SC porous titanium cervical interbody fusion system. The standalone system, like all Tesera implants, is fabricated via additive manufacturing (3D printing) to create a highly-porous surface structure.
Smith & Nephew
Joint | Commenced U.S. limited launch of the REDAPT™ Revision Acetabular Fully Porous Cup with CONCELOC™ technology, its 1st 3D-printed titanium hip implant.
Spineart
Spine | Received CE Mark Approval for its JULIET®Ti lumbar interbody systems featuring TI-LIFE, a micro-porous scaffold designed to mimic trabecular bone. Produced via additive manufacturing, TI-LIFE features interconnected pores of 600 μm to 700 μm with an overall porosity of 70% to 75%, and is designed to enable cell colonization and promote bone in-growth.
Stryker
Spine | Announced FDA 510(k) clearance (and subsequent launch) of Tritanium® PL, a highly-porous posterior lumbar cage made via 3D additive manufacturing.
Spine | Results from a pre-clinical interbody fusion study of Stryker Spine’s 3D-printed Tritanium PL Interbody Cage demonstrated statistically superior range of motion, bone in-growth profile and greater average construct stiffness vs. PEEK and titanium plasma-sprayed PEEK cages.
“For the foreseeable future, at least the next three, four years or so, our focus is on innovative new products and not replacing our existing products with 3D printed products. The pipeline of innovative new geometries that can’t be made without 3D printing is the area of focus. It’s not about trying to replace our products and drive down cost. Over time, ten years from now, that could be the case, but in the near- to mid-term, it’s really a focus on innovative new products.”
—William R. Jellison, Stryker’s Vice President and Chief Financial Officer (retired)
“We’re seeing [3D printing] impact two different divisions of Stryker: our knee business as well as spine, and we have a huge line-up of other divisions with ideas and prototypes to get into 3D printed titanium products.”
—Kevin Lobo, Stryker’s Chief Executive Officer
Zimmer Biomet (LDR)
Spine | Poly-Shape, a French manufacturing company specializing in laser sintering, entered into an exclusive agreement with LDR. The agreement combines LDR’s spinal focus and approach to implant design with Poly-Shape’s proprietary, additive manufacturing methods. The agreement was signed in 4Q15. Initial projects are underway, with the expectation to launch newly-designed spinal implants produced with Poly-Shape technology as early as mid-2017.
“What we are definitely looking for is patient-specific implants; how do we make implants which are complicated—not necessarily off the shelf—but where we would be taking information from a patient’s image and making an implant for that. We see a big application in that field.”
—Mukesh Kumar, Ph.D., Director, Advanced Process Technology, Zimmer Biomet
Other notable comments:
Andy Christensen, Additive Manufacturing Veteran
FDA first cleared an additively-manufactured 3D printed metal implant in 2010, and implants were 3D printed in Europe prior to that. FDA says that they’ve cleared ~80 devices that are 3D-printed medical devices. I think from their standpoint that this includes plastic parts as well as metal parts. Many experts predict that 3D printing in medical implants is going to grow by 20%+ over the next 5, 7, 10 years.
Bob Kinsella, President, Kinsella Group
Based on his perspective from working with manufacturers that are experimenting with it, Kinsella observed that additive manufacturing won’t be fully realized until companies get past viewing it as simply a tool and implement it for actual production of parts. Once that takes place, the technology or the human expertise associated with it will be ripe for more M&A activity at device and supplier company levels.
Earlier this year, a Member sent us a question: What portion of new products introduced in joint reconstruction and spine are additively manufactured?
This question had been on our radar for some time. Additive manufacturing (AM) has generated more interest than any other topic we’ve written about or presented at OMTEC in the last two...
Earlier this year, a Member sent us a question: What portion of new products introduced in joint reconstruction and spine are additively manufactured?
This question had been on our radar for some time. Additive manufacturing (AM) has generated more interest than any other topic we’ve written about or presented at OMTEC in the last two years. Internally, we’ve wondered, is it just buzz or are companies actually adopting the technology? To investigate, we tracked products launches and regulatory announcements from January 2015 to 2017. Nearly two dozen companies were mentioned in ORTHOFLASH® during this time period. For your benefit, we’ve listed these companies, their market segments and products below. We’ve also included executive insight that we found to be valuable.
Our analysis leads us to state that >5% of joint reconstruction and spine products launched or about to be launched in the last two years incorporate additive manufacturing.
Work still needs to be done. This is not a comprehensive list of companies using the technology, nor does it represent all AM-related products on the market, but it is a start. We expect that more device and supplier companies will adopt additive manufacturing once more regulatory guidelines are established and patient outcome evidence is generated.
4WEB
Spine | Commenced U.S. launch of 3D-printed Posterior Spine Truss system of interbody fusion devices, with applications including PLIF, TLIF and Oblique procedures.
Amedica
Spine | Fabricated its first silicon nitride structures with a 3D printing process called robotic deposition, or robocasting. The products have been scanned with electron microscopy to confirm integrity and validity of the additive manufacturing method, and have demonstrated similar theoretical density and microstructure attributes to traditionally-manufactured silicon nitride fusion devices currently in use.
Beijing AK Medical
Joint | Received approval by the Chinese State FDA for the 3D ACT hip system, reportedly the first approval in China for an additively-manufactured orthopaedic implant.
ConforMIS
Joint | Commenced full commercial launch of the iTotal PS customized posterior stabilized total knee. The company’s knee implants and instrumentation are manufactured additively.
Joint | Introduced the next-gen iTotal CR (cruciate-retaining) total knee, designed to further reduce intraoperative steps during knee replacement.
EIT/Emerging Implant Technologies
Spine | Announced the first patient treated with an anatomically-adapted 3D printed titanium fusion implant, in a case of cervical spine degeneration.
Globus Medical
Spine | Investing in 3D printing equipment, but sees it as best applied to custom implants for scoliosis or anatomic abnormalities; not seeing benefit of 3D-printed implants for the vast majority of procedures, especially as many manufacturers utilize surface coatings that support bony ongrowth
HT Medical
Spine | Development pipeline includes products based on proprietary 3D-printed titanium additive technology from Additive Innovations
Johnson & Johnson
n/a | Sandi Peterson, Executive Vice President, Group Worldwide Chairman, explained how JNJ is an enterprise entity that can offer broad services to customers. This is the foundation for how they will win—using size and scale to serve hospitals and patients. Pieces of the strategy include use of technology to reduce development cycles, employ advanced analytics to get real-time views on data (which can be echoed company-wide), and harness capabilities like 3D printing. (They just announced a new partnership with HP.)
joimax
Spine | Launched the EndoLIF® On-Cage for spinal stabilization and fusion in the U.S. The 3D-printed titanium alloy EndoLIF On-Cage supports a mini-open or an inter-muscular approach.
K2M
Spine | Received FDA 510(k) clearances to market CASCADIA™ Cervical and CASCADIA AN Lordotic Oblique Interbody systems, featuring Lamellar 3D-printed Titanium Technology™.
Lima
Joint | Launched SMR® Stemless for its shoulder replacement portfolio, combining modularity and a proprietary Trabecular Titanium structure. Produced with additive manufacturing through electron beam melting, SMR Stemless features a 3D structure designed to imitate natural bone with clinically-proven osteointegration.
Medacta
Spine | Completed initial U.S. surgeries using its proprietary 3D-printed MySpine Patient Matched Technology Low Profile Guide, following FDA clearance.
Medicrea
Spine | Filed its FDA 510(k) submission for 3D-printed titanium interbody devices with compatible UNiD™ Lab surgical planning and analytical services.
Mighty Oak Medical
Spine | Received a second FDA 510(k) clearance for FIREFLY® Pedicle Screw Navigation Guides, extending compatibility to essentially all currently cleared pedicle screw systems and extending indications to include the T1-S2/ilium region. FIREFLY comprises patient-matched bone models and intra-op pedicle screw guides created via 3D printing.
NextStep Arthropedix
Joint | Received FDA 510(k) clearance for the iNSitu cementless total hip, additively manufactured via Electron Beam Melting; includes a highly cross-linked Vitamin E UHMWPE bearing
Nexxt Spine
Spine | Launched the DT Elite Guide System, intended to reduce the number of operative steps and simplify anterior cervical discectomy and fusion. DT Elite, manufactured through 3D printing technology, bridges a gap between the company’s Struxxure Anterior Cervical Plate and Honour Cervical Interbody systems.
Spine | Developing NanoMatrixx, 3D printed porous bioactive titanium material designed to actively participate in intervertebral fusion. NanoMatrixx’s micro and nanosurface topography with 70% porosity is intended to stimulate mesenchymal stem cells to differentiate into bone-forming osteoblasts.
Orthofix
Spine | Announced FDA 510(k) clearance and U.S. limited launch of the FORZA® PTC™ (PEEK Titanium Composite) Spacer. The system features PEEK and 3D-printed titanium endplates for use in lumbar spinal fusion to treat degenerative disc disease.
Oxford Performance Materials
Spine | Received FDA 510(k) clearance to market the SpineFab® VBR implant, reportedly the first FDA-cleared 3D-printed load-bearing polymer device for long-term implantation.
Renovis
Spine | Received FDA 510(k) clearance to market the Tesera™ SC porous titanium cervical interbody fusion system. The standalone system, like all Tesera implants, is fabricated via additive manufacturing (3D printing) to create a highly-porous surface structure.
Smith & Nephew
Joint | Commenced U.S. limited launch of the REDAPT™ Revision Acetabular Fully Porous Cup with CONCELOC™ technology, its 1st 3D-printed titanium hip implant.
Spineart
Spine | Received CE Mark Approval for its JULIET®Ti lumbar interbody systems featuring TI-LIFE, a micro-porous scaffold designed to mimic trabecular bone. Produced via additive manufacturing, TI-LIFE features interconnected pores of 600 μm to 700 μm with an overall porosity of 70% to 75%, and is designed to enable cell colonization and promote bone in-growth.
Stryker
Spine | Announced FDA 510(k) clearance (and subsequent launch) of Tritanium® PL, a highly-porous posterior lumbar cage made via 3D additive manufacturing.
Spine | Results from a pre-clinical interbody fusion study of Stryker Spine’s 3D-printed Tritanium PL Interbody Cage demonstrated statistically superior range of motion, bone in-growth profile and greater average construct stiffness vs. PEEK and titanium plasma-sprayed PEEK cages.
“For the foreseeable future, at least the next three, four years or so, our focus is on innovative new products and not replacing our existing products with 3D printed products. The pipeline of innovative new geometries that can’t be made without 3D printing is the area of focus. It’s not about trying to replace our products and drive down cost. Over time, ten years from now, that could be the case, but in the near- to mid-term, it’s really a focus on innovative new products.”
—William R. Jellison, Stryker’s Vice President and Chief Financial Officer (retired)
“We’re seeing [3D printing] impact two different divisions of Stryker: our knee business as well as spine, and we have a huge line-up of other divisions with ideas and prototypes to get into 3D printed titanium products.”
—Kevin Lobo, Stryker’s Chief Executive Officer
Zimmer Biomet (LDR)
Spine | Poly-Shape, a French manufacturing company specializing in laser sintering, entered into an exclusive agreement with LDR. The agreement combines LDR’s spinal focus and approach to implant design with Poly-Shape’s proprietary, additive manufacturing methods. The agreement was signed in 4Q15. Initial projects are underway, with the expectation to launch newly-designed spinal implants produced with Poly-Shape technology as early as mid-2017.
“What we are definitely looking for is patient-specific implants; how do we make implants which are complicated—not necessarily off the shelf—but where we would be taking information from a patient’s image and making an implant for that. We see a big application in that field.”
—Mukesh Kumar, Ph.D., Director, Advanced Process Technology, Zimmer Biomet
Other notable comments:
Andy Christensen, Additive Manufacturing Veteran
FDA first cleared an additively-manufactured 3D printed metal implant in 2010, and implants were 3D printed in Europe prior to that. FDA says that they’ve cleared ~80 devices that are 3D-printed medical devices. I think from their standpoint that this includes plastic parts as well as metal parts. Many experts predict that 3D printing in medical implants is going to grow by 20%+ over the next 5, 7, 10 years.
Bob Kinsella, President, Kinsella Group
Based on his perspective from working with manufacturers that are experimenting with it, Kinsella observed that additive manufacturing won’t be fully realized until companies get past viewing it as simply a tool and implement it for actual production of parts. Once that takes place, the technology or the human expertise associated with it will be ripe for more M&A activity at device and supplier company levels.
You are out of free articles for this month
Subscribe as a Guest for $0 and unlock a total of 5 articles per month.
You are out of five articles for this month
Subscribe as an Executive Member for access to unlimited articles, THE ORTHOPAEDIC INDUSTRY ANNUAL REPORT and more.
JV
Julie Vetalice is ORTHOWORLD's Editorial Assistant. She has covered the orthopedic industry for over 20 years, having joined the company in 1999.