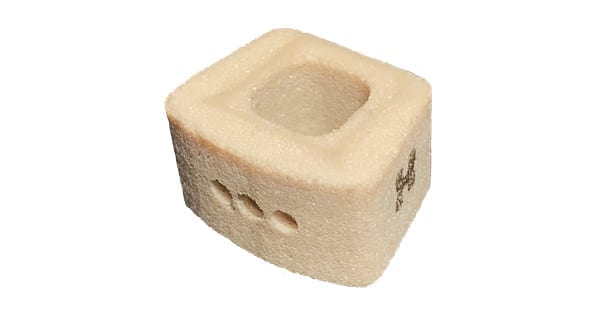
HAPPE Spine received notice of allowance from the U.S. Patent and Trademark Office for U.S. Pat. App. No. 14/078,614, providing broad protections for material and manufacturing techniques that support its fully porous, bioactive polyetheretherketone technology.
The technology combines characteristics of porosity and bioactivity into a strong, radiolucent material with skeletal versatility. The manufacturing method allows the implant density or porosity to be varied to optimize both osteointegration and biomechanical loading.
HAPPE implants are made with a proprietary molding method that leverages traditional processes. The technology also leverages surgeons’ current processes, thus eliminating a learning curve.
Ryan K. Roeder, Ph.D. of the University of Notre Dame, with HAPPE’s engineering team, conceptualized modifying PEEK to be both porous and bioactive for orthopedic applications throughout the body.
Dr. Roeder said, “A key to our technology, recognized in this patent, is that our hydroxyapatite particles are exposed on pore surfaces creating a hydrophilic, micro-roughened and bioactive surface that promotes bone ingrowth. Furthermore, due to a whisker-like shape, our hydroxyapatite particles are firmly embedded in the PEEK matrix for long-term bioactivity and mechanical reinforcement.”
Doug Snell, Engineering Director at HAPPE Spine said, “It is exciting to see all aspects of the HAPPE porous PEEK technology coming to fruition in our cervical interbody implant, which is the first of our many spine and orthopedic product applications. The proprietary forming process, which Dr. Roeder proved out at the University of Notre Dame, has now been implemented into a production environment that meets all future growth needs. Forming a contiguous construct of load-bearing dense hydroxyapatite PEEK seamlessly integrated into a 75% porous HA PEEK scaffold is a challenging task. Our team has come together and created a robust process that forms this complex structure reliably and it is now a highly scalable production process able to meet the industry standard and it’s demand.”
HAPPE Spine received notice of allowance from the U.S. Patent and Trademark Office for U.S. Pat. App. No. 14/078,614, providing broad protections for material and manufacturing techniques that support its fully porous, bioactive polyetheretherketone technology.
The technology combines characteristics of porosity and bioactivity into a...
HAPPE Spine received notice of allowance from the U.S. Patent and Trademark Office for U.S. Pat. App. No. 14/078,614, providing broad protections for material and manufacturing techniques that support its fully porous, bioactive polyetheretherketone technology.
The technology combines characteristics of porosity and bioactivity into a strong, radiolucent material with skeletal versatility. The manufacturing method allows the implant density or porosity to be varied to optimize both osteointegration and biomechanical loading.
HAPPE implants are made with a proprietary molding method that leverages traditional processes. The technology also leverages surgeons’ current processes, thus eliminating a learning curve.
Ryan K. Roeder, Ph.D. of the University of Notre Dame, with HAPPE’s engineering team, conceptualized modifying PEEK to be both porous and bioactive for orthopedic applications throughout the body.
Dr. Roeder said, “A key to our technology, recognized in this patent, is that our hydroxyapatite particles are exposed on pore surfaces creating a hydrophilic, micro-roughened and bioactive surface that promotes bone ingrowth. Furthermore, due to a whisker-like shape, our hydroxyapatite particles are firmly embedded in the PEEK matrix for long-term bioactivity and mechanical reinforcement.”
Doug Snell, Engineering Director at HAPPE Spine said, “It is exciting to see all aspects of the HAPPE porous PEEK technology coming to fruition in our cervical interbody implant, which is the first of our many spine and orthopedic product applications. The proprietary forming process, which Dr. Roeder proved out at the University of Notre Dame, has now been implemented into a production environment that meets all future growth needs. Forming a contiguous construct of load-bearing dense hydroxyapatite PEEK seamlessly integrated into a 75% porous HA PEEK scaffold is a challenging task. Our team has come together and created a robust process that forms this complex structure reliably and it is now a highly scalable production process able to meet the industry standard and it’s demand.”
You are out of free articles for this month
Subscribe as a Guest for $0 and unlock a total of 5 articles per month.
You are out of five articles for this month
Subscribe as an Executive Member for access to unlimited articles, THE ORTHOPAEDIC INDUSTRY ANNUAL REPORT and more.
JV
Julie Vetalice is ORTHOWORLD's Editorial Assistant. She has covered the orthopedic industry for over 20 years, having joined the company in 1999.