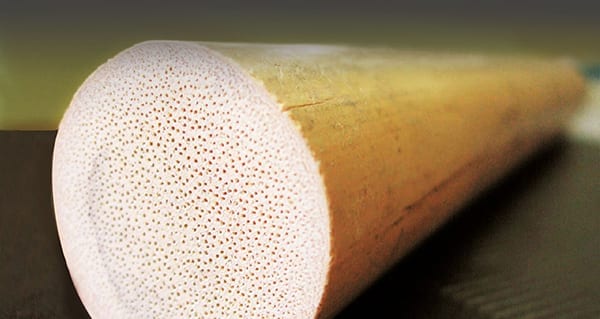
For many people, a large bone defect caused by disease, trauma, infection or other sources can be a life-long impediment to full functionality. Today’s treatments are limited, often requiring several surgeries with inconsistent results.
Most patients experience a long journey in bone reconstruction. Some, including children, don’t have a bone substitute that will follow the growth of the natural bone.
GreenBone Ortho, based in Faenza, Italy, seeks to change that with an innovative approach to bone regeneration. They’re using technology originating from research at the National Council Institute that mimics nature to create a long-term solution using rattan, a type of wood, as the base material.
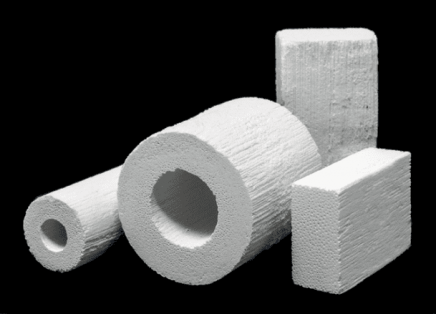
GreenBone established a manufacturing line that allows them to process rattan wood for its bone substitute technology.
“The research explores nature as a source of inspiration for a new biomaterial that, in principle, should not only be biocompatible and suitable to be integrated into the body but indeed able to enter a regenerative process, especially for larger bone defects,” said Lorenzo Pradella, Co-founder and Chief Executive Officer of GreenBone. “They started in the lab with the knowledge that there were very few species of wood with an internal 3D architecture, in terms of channel-like porosity, both longitudinal and interconnected, very closely mimicking the internal organization of human bone. They’ve developed a technology that originated the first patent demonstrating the possibility to transform wood into bone biomimetic materials.”
GreenBone was launched based on this initial research, becoming operational in 2015 with the objective of commercializing the lab-based process and demonstrate the possibility of obtaining a product that can be effectively manufactured.
The Technology
GreenBone established a manufacturing line that allows them to use rattan wood, which is the closest material to mimicking human bone architecture with the right characteristics, and shape it accordingly with a piece of bone that they want to reconstruct. Then, their process allows a complete chemical transformation of the natural material into the final product with a chemical composition reproducing that of the human bone matrix.
“It’s a combination of hydroxyapatite, beta-tricalcium phosphate, and some ions such as magnesium and strontium, but without losing in any step of the process this beautiful internal architecture that is provided by nature,” Mr. Pradella said. “The final bone-maker product has channel-like porosity from the macro to the nanoscale, both longitudinally and interconnected, coming from wood, but with the chemistry completely different indeed. The final product does not retain atoms from the original piece of wood.”
The solution is not a coating, but rather a real chemical transformation of the material itself, called biomorphic transformation. Shaped rattan samples (hollow cylinder, blocks, etc.) are treated at a very high temperature in the absence of oxygen in a process that allows GreenBone to extract the skeleton of pure carbon from the natural wood.
Then, a five-step reaction occurs to achieve the final composition. In this way, the architecture is preserved entirely, but the chemistry is completely changed. When the carbon is replaced, no atoms remain from the original piece of wood.
The Difference
Today’s options include bone transplantation (the gold standard), cadaver bones and synthetic bone substitutes. GreenBone is offering an alternative.
“All ceramic bone substitutes today are made of hydroxyapatite and calcium phosphate starting from powder,” Mr. Pradella said. “A process called sintering has to be applied in order to substantially melt the powder and aggregate it, if the objective is to have a block even for small dimension. But sintering creates big macro-crystals that are not suitable to be metabolized by cells.”
GreenBone technology creates hydroxyapatite on an existing 3D architecture, so it doesn’t require sintering. This process preserves the nanocrystal bioactive morphology of hydroxyapatite, which is the one that cells are able to metabolize effectively.
The purpose of the technology is osseointegrative and osteoconductive when introduced into the body, but also to be strongly osteoinductive and able to sustain a regeneration process that occurs through a progressive physiological resorption of the implant and replacement by new bone matrix with proper revascularization. So, the patient would in effect be regrowing their own bone.
“This is what we have observed during the preclinical development, including an important study in large animals that has demonstrated the properties of GreenBone in terms of osseointegration, osteoconduction, and osteoinduction, and showing resorption and regeneration,” Mr. Pradella said.
What’s Next
GreenBone’s development has been completed in compliance with European regulation. They obtained approval under the CE Mark in December 2019. The first indication of use is in a patient with bone loss caused by trauma or surgically used in the extremities and the pelvis.
“We have different shapes and sizes available in terms of hollow cylinders that reproduce exactly the structure of long bones, including the medullary canal, and blocks,” Mr. Pradella said. “We are in the process of developing other shapes. We have also completed FDA submission and hope to get approval by the end of 2020.”
GreenBone is also conducting two clinical studies in Europe. The first focuses on long bones in arms and legs with defects up to 3 centimeters in the first part of the study, and later, will be up to 6 centimeter defects in the second part of the study. The second study is for reconstruction of iliac crest defects. In total, GreenBone has 13 patients recruited in studies with positive follow-up.
One of the most important objectives for GreenBone is to further scale-up manufacturing to the level needed for the market. Both the product and the process are patent-protected in Europe, the U.S., and other strategic territories.
The bone substitute market itself is around $3 billion, combining Europe and the U.S., based on the number of bone substitutes sold in the market, according to TechNavio.
“Still today, let’s say between 30% and 50% of patients are subjected to bone transplantation, or autograft,” Mr. Pradella said. “There is a weakness in the capacity in alternatives able to regenerate and behave like natural bone in the clinic. And our objective is to bring a new material that can have the ambition to expand the market in a way to be used for at least some of the patients that would have been subjected to bone transplantation.”
With this in mind, GreenBone aims to be one of the market leaders in bone reconstructive surgery.
The technology is considered to be a platform technology, because starting from wood, it can attain any shape.
“We emphasize GreenBone as a solution for any bone reconstructive surgery where a bone substitute is needed,” Mr. Pradella said. “The next step will be for us to develop the product in spine and maxillofacial reconstruction, bone infection and cancer, which are the other two largest market opportunities for a product like this.”
GreenBone is using this year to expand the clinical use of the product in Europe. At the same time, they are focusing on expanding their manufacturing capacity to be able to sustain commercialization. Their goal is to consider the U.S. market beginning in 2022.
“We believe that the home of revolution is repair and regenerate at the same time,” Mr. Pradella said. “This is our mission and our vision on how we believe that innovative products should behave in this very important segment, combining that with the ambition to provide a unique solution to both patients and surgeons.”
For many people, a large bone defect caused by disease, trauma, infection or other sources can be a life-long impediment to full functionality. Today’s treatments are limited, often requiring several surgeries with inconsistent results.
Most patients experience a long journey in bone reconstruction. Some, including children, don’t have a bone...
For many people, a large bone defect caused by disease, trauma, infection or other sources can be a life-long impediment to full functionality. Today’s treatments are limited, often requiring several surgeries with inconsistent results.
Most patients experience a long journey in bone reconstruction. Some, including children, don’t have a bone substitute that will follow the growth of the natural bone.
GreenBone Ortho, based in Faenza, Italy, seeks to change that with an innovative approach to bone regeneration. They’re using technology originating from research at the National Council Institute that mimics nature to create a long-term solution using rattan, a type of wood, as the base material.
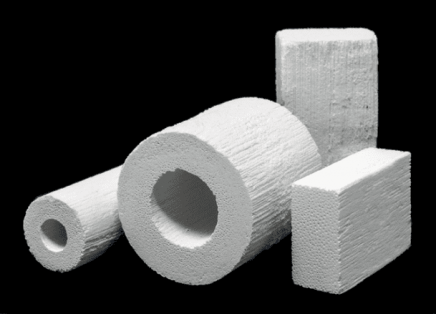
GreenBone established a manufacturing line that allows them to process rattan wood for its bone substitute technology.
“The research explores nature as a source of inspiration for a new biomaterial that, in principle, should not only be biocompatible and suitable to be integrated into the body but indeed able to enter a regenerative process, especially for larger bone defects,” said Lorenzo Pradella, Co-founder and Chief Executive Officer of GreenBone. “They started in the lab with the knowledge that there were very few species of wood with an internal 3D architecture, in terms of channel-like porosity, both longitudinal and interconnected, very closely mimicking the internal organization of human bone. They’ve developed a technology that originated the first patent demonstrating the possibility to transform wood into bone biomimetic materials.”
GreenBone was launched based on this initial research, becoming operational in 2015 with the objective of commercializing the lab-based process and demonstrate the possibility of obtaining a product that can be effectively manufactured.
The Technology
GreenBone established a manufacturing line that allows them to use rattan wood, which is the closest material to mimicking human bone architecture with the right characteristics, and shape it accordingly with a piece of bone that they want to reconstruct. Then, their process allows a complete chemical transformation of the natural material into the final product with a chemical composition reproducing that of the human bone matrix.
“It’s a combination of hydroxyapatite, beta-tricalcium phosphate, and some ions such as magnesium and strontium, but without losing in any step of the process this beautiful internal architecture that is provided by nature,” Mr. Pradella said. “The final bone-maker product has channel-like porosity from the macro to the nanoscale, both longitudinally and interconnected, coming from wood, but with the chemistry completely different indeed. The final product does not retain atoms from the original piece of wood.”
The solution is not a coating, but rather a real chemical transformation of the material itself, called biomorphic transformation. Shaped rattan samples (hollow cylinder, blocks, etc.) are treated at a very high temperature in the absence of oxygen in a process that allows GreenBone to extract the skeleton of pure carbon from the natural wood.
Then, a five-step reaction occurs to achieve the final composition. In this way, the architecture is preserved entirely, but the chemistry is completely changed. When the carbon is replaced, no atoms remain from the original piece of wood.
The Difference
Today’s options include bone transplantation (the gold standard), cadaver bones and synthetic bone substitutes. GreenBone is offering an alternative.
“All ceramic bone substitutes today are made of hydroxyapatite and calcium phosphate starting from powder,” Mr. Pradella said. “A process called sintering has to be applied in order to substantially melt the powder and aggregate it, if the objective is to have a block even for small dimension. But sintering creates big macro-crystals that are not suitable to be metabolized by cells.”
GreenBone technology creates hydroxyapatite on an existing 3D architecture, so it doesn’t require sintering. This process preserves the nanocrystal bioactive morphology of hydroxyapatite, which is the one that cells are able to metabolize effectively.
The purpose of the technology is osseointegrative and osteoconductive when introduced into the body, but also to be strongly osteoinductive and able to sustain a regeneration process that occurs through a progressive physiological resorption of the implant and replacement by new bone matrix with proper revascularization. So, the patient would in effect be regrowing their own bone.
“This is what we have observed during the preclinical development, including an important study in large animals that has demonstrated the properties of GreenBone in terms of osseointegration, osteoconduction, and osteoinduction, and showing resorption and regeneration,” Mr. Pradella said.
What’s Next
GreenBone’s development has been completed in compliance with European regulation. They obtained approval under the CE Mark in December 2019. The first indication of use is in a patient with bone loss caused by trauma or surgically used in the extremities and the pelvis.
“We have different shapes and sizes available in terms of hollow cylinders that reproduce exactly the structure of long bones, including the medullary canal, and blocks,” Mr. Pradella said. “We are in the process of developing other shapes. We have also completed FDA submission and hope to get approval by the end of 2020.”
GreenBone is also conducting two clinical studies in Europe. The first focuses on long bones in arms and legs with defects up to 3 centimeters in the first part of the study, and later, will be up to 6 centimeter defects in the second part of the study. The second study is for reconstruction of iliac crest defects. In total, GreenBone has 13 patients recruited in studies with positive follow-up.
One of the most important objectives for GreenBone is to further scale-up manufacturing to the level needed for the market. Both the product and the process are patent-protected in Europe, the U.S., and other strategic territories.
The bone substitute market itself is around $3 billion, combining Europe and the U.S., based on the number of bone substitutes sold in the market, according to TechNavio.
“Still today, let’s say between 30% and 50% of patients are subjected to bone transplantation, or autograft,” Mr. Pradella said. “There is a weakness in the capacity in alternatives able to regenerate and behave like natural bone in the clinic. And our objective is to bring a new material that can have the ambition to expand the market in a way to be used for at least some of the patients that would have been subjected to bone transplantation.”
With this in mind, GreenBone aims to be one of the market leaders in bone reconstructive surgery.
The technology is considered to be a platform technology, because starting from wood, it can attain any shape.
“We emphasize GreenBone as a solution for any bone reconstructive surgery where a bone substitute is needed,” Mr. Pradella said. “The next step will be for us to develop the product in spine and maxillofacial reconstruction, bone infection and cancer, which are the other two largest market opportunities for a product like this.”
GreenBone is using this year to expand the clinical use of the product in Europe. At the same time, they are focusing on expanding their manufacturing capacity to be able to sustain commercialization. Their goal is to consider the U.S. market beginning in 2022.
“We believe that the home of revolution is repair and regenerate at the same time,” Mr. Pradella said. “This is our mission and our vision on how we believe that innovative products should behave in this very important segment, combining that with the ambition to provide a unique solution to both patients and surgeons.”
You are out of free articles for this month
Subscribe as a Guest for $0 and unlock a total of 5 articles per month.
You are out of five articles for this month
Subscribe as an Executive Member for access to unlimited articles, THE ORTHOPAEDIC INDUSTRY ANNUAL REPORT and more.
HT
Heather Tunstall is an ORTHOWORLD Contributor and owner of Tunstall Content.