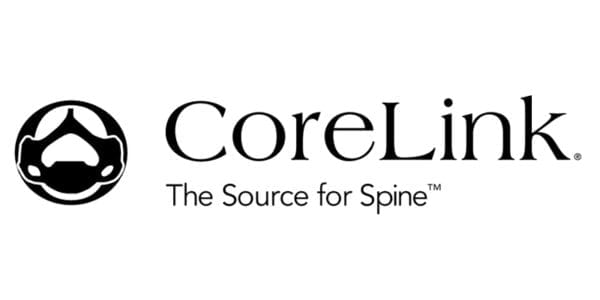
CoreLink has implanted over 5,000 3D-printed devices that employ their proprietary Mimetic Metal® additively-manufactured technology. The first implantation occurred in 2017.
Mimetic Metal combines a lattice framework and inner trabecular pores to mimic the structural, functional and physiological properties of bone. The design creates anisotropic stiffness to aid in load transfer. Further, open-pore architecture provides hydrophilic wicking capabilities to allow blood flow through the implant. The titanium alloy support structure also minimizes overall implant density, resulting in beneficial imaging characteristics.
CoreLink’s Mimetic Metal offerings include the M3 Stand-Alone ALIF and F3D family of implants. F3D interbodies include curved, straight, anterior lumbar, cervical and lateral designs in an range of footprints, heights and lordosis.
“CoreLink set out to emulate nature with our 3D-printed technology. Our unique design has enabled us to optimize everything needed in an interbody device – imaging, graft capacity, porosity, load sharing, strength, and stiffness,” said Jay Bartling, CEO, CoreLink. “From the development of the technology to execution of the 3D printing, we design and manufacture Mimetic Metal implants in our facility, ensuring both form and function are met to help patients in their healing process.”
CoreLink has implanted over 5,000 3D-printed devices that employ their proprietary Mimetic Metal® additively-manufactured technology. The first implantation occurred in 2017.
Mimetic Metal combines a lattice framework and inner trabecular pores to mimic the structural, functional and physiological properties of bone. The design creates...
CoreLink has implanted over 5,000 3D-printed devices that employ their proprietary Mimetic Metal® additively-manufactured technology. The first implantation occurred in 2017.
Mimetic Metal combines a lattice framework and inner trabecular pores to mimic the structural, functional and physiological properties of bone. The design creates anisotropic stiffness to aid in load transfer. Further, open-pore architecture provides hydrophilic wicking capabilities to allow blood flow through the implant. The titanium alloy support structure also minimizes overall implant density, resulting in beneficial imaging characteristics.
CoreLink’s Mimetic Metal offerings include the M3 Stand-Alone ALIF and F3D family of implants. F3D interbodies include curved, straight, anterior lumbar, cervical and lateral designs in an range of footprints, heights and lordosis.
“CoreLink set out to emulate nature with our 3D-printed technology. Our unique design has enabled us to optimize everything needed in an interbody device – imaging, graft capacity, porosity, load sharing, strength, and stiffness,” said Jay Bartling, CEO, CoreLink. “From the development of the technology to execution of the 3D printing, we design and manufacture Mimetic Metal implants in our facility, ensuring both form and function are met to help patients in their healing process.”
You are out of free articles for this month
Subscribe as a Guest for $0 and unlock a total of 5 articles per month.
You are out of five articles for this month
Subscribe as an Executive Member for access to unlimited articles, THE ORTHOPAEDIC INDUSTRY ANNUAL REPORT and more.
JV
Julie Vetalice is ORTHOWORLD's Editorial Assistant. She has covered the orthopedic industry for over 20 years, having joined the company in 1999.