Call it additive or 3D printing, embrace or eschew it, there is no getting around the reality that the technology is a big deal in orthopaedics.
What follows is by no means a complete representation of all companies that engage this process, but rather a roundup of companies that made headlines within 2017.
Joint Replacement
Bodycad received product notification confirmation which enables them to commercially launch their Unicompartmental Knee System within the European Union. Bodycad employs three types of 3D printing technologies—metal, plastic and multi-color modeling/prototyping—to create its implants.
ConforMISÂ received FDA 510(k) clearance of the iTotal Hip replacement system. Limited launch is slated for 2H18. iTotal employs single-use 3D printed instruments.
Corin and Ossis entered a joint venture agreement to develop patient-specific hip and knee implants. The agreement combines Corin’s technologies, such as 3D printing and the Optimized Positioning System, that will complement Ossis’ experience in custom-made implants.
In 1Q17, Lima Corporate celebrated ten years using its proprietary Trabecular Titanium 3D printing technology. (It started with the Delta TT acetabular cup.) In 2Q, the company marked the 15th anniversary of its SMR modular shoulder system by launching SMR bone graft instruments and Lima Personalized Surgical Instruments. At the end of 3Q17, the company announced the milestone of 100,000 implantations of the SMR shoulder system.
Materialise received FDA 510(k) clearance to market its Surgicase Orthopaedics system to assist in pre-op planning for pediatric patients undergoing radius or ulna osteotomy. The system comprises SurgiCase Connect surgical planning software and patient-specific SurgiCase Guides, which are 3D printed.
Medacta received FDA 510(k) clearance and completed first knee revision procedures with 3DMetal Tibial Cones.
Stryker received FDA 510(k) clearance to market the Mako total knee application with Triathlon cementless components; the Tritanium tibial baseplate and metal-backed patella components are built with Stryker’s AMagine additive manufacturing technology. GE Additive and Stryker established an agreement to support Stryker’s growth in additive manufacturing, covering new machines, materials and services.
Spine
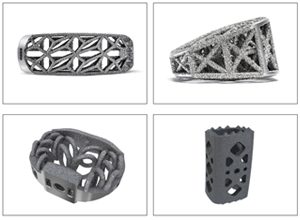
Left to right: 4WEB Medical – Lateral Spine Truss and 3D-printed Anterior Spine Truss Interbody Fusion Systems
Studies indicate that 4WEB Medical’s Lateral Spine Truss demonstrated a better resistance to subsidence vs. an annular interbody implant. The findings indicate the capacity for load distribution inherent to 4WEB’s additively-manufactured truss technology. The company also launched its next-generation 3D-printed Anterior Spine Truss interbody fusion system.
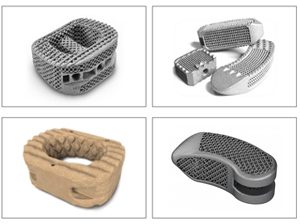
Left to right: ChoiceSpine – HAWKEYE Ti 3D VBR
Camber Spine Technologies – SPIRA Open Matrix ALIF Device
Camber Spine Technologies received FDA 510(k) clearance and commenced U.S. launch of the SPIRA Open Matrix ALIF device, manufactured with additive techniques.
ChoiceSpine received FDA 510(k) clearance to market and announced first clinical use of the HAWKEYE Ti 3D-printed titanium vertebral body replacement, its first 3D-printed device.
Emerging Implant Technologies acquired a portfolio of 22 issued and pending patents covering 3D printed expandable spinal fusion cages, and received FDA 510(k) clearance for 3D-printed spinal interbody devices to address ALIF, PLIF, TLIF and cervical procedures.
HD LifeSciences received FDA 510(k) clearance and commenced U.S. launch of NanoHive, a system of interbody devices for ALIF, PLIF and TLIF procedures. The devices are based on HD’s proprietary, additively-manufactured Soft Titanium™ honeycomb lattice material.
K2M entered into development and supply agreements with 3D Systems that entail an exclusive software solutions partnership and production capacity to support the manufacture of CASCADIA Interbody systems, which feature Lamellar 3D Titanium technology. K2M also acquired exclusive license to a portfolio of 17 patents for expandable interbody fusion devices for development of new products using Lamellar 3D. Finally, the company announced FDA 510(k) clearance of MOJAVE PL, a 3D-printed expandable posterior lumbar interbody system. (3D-printed AND expandable AND FDA-cleared—that was a market first!)
Medicrea received FDA 510(k) clearance to market IB3D 3D-printed interbody devices, and introduced its AdapTEK in-house additive manufacturing technology.
OrthoPediatrics entered into an agreement for exclusive U.S. distribution of Mighty Oak Medical’s FIREFLY pedicle screw navigation guides in pediatric hospitals. FIREFLY guides are 3D-printed, disposable and patient-specific.
Nexxt Spine received FDA 510(k) clearance to market 3D-printed NEXXT MATRIXX interbody and vertebral body replacement devices.
NuVasive unveiled its Advanced Materials Science portfolio, including the 3D-printed titanium Modulus XLIF and porous PEEK technology acquired with its purchase of Vertera Spine.
Renovis Surgical received FDA 510(k) clearance to market Tesera 3D-printed posterior lumbar interbody fusion systems.
RTI Surgical launched the Fortilink-C IBF system, its first device featuring TETRAfuse 3D-printed polymer material.
Stryker Spine received FDA 510(k) clearance and launched its 3D-printed Tritanium C Anterior Cervical Cage.
Trauma
Additive Orthopaedics received FDA 510(k) clearance for its Bunion Correction System and Locking Lattice plate, both constructed via 3D printing. The company also launched a multi-center clinical trial to measure bone in-growth into 3D-printed bone segments.
DePuy Synthes acquired 3D printing technology from Tissue Regeneration Systems to offer patient-specific, bioresorbable implants for orthopaedic and CMF applications.
Supplier News
Arcam will evaluate strategic alternatives regarding its DiSanto Technology contract manufacturing subsidiary (DTI), in efforts to strengthen DTI’s ability to serve as a contract manufacturing partner to orthopaedic customers seeking to combine additive and traditional manufacturing capabilities. Arcam will consider restructuring of DTI, a full or partial separation via a spin-off, sale, joint venture, strategic collaboration or other transaction. (Arcam purchased DTI in 2014 for US $15.8MM; GE purchased Arcam in late 2016.)
ASTM International seeks to establish a center of excellence in additive manufacturing. The entity—an international standards organization that develops and publishes voluntary consensus technical standards for a range of materials, products, systems and services—has called for industry/university proposals aimed at creating a global innovation hub advancing AM technical standards, related R&D, education, training, etc. Further, the center will serve as a consortium in attracting stakeholders from medical and various other industries that are increasingly engaged in AM applications. The winning proposal will be announced in early 2018.
Testing data indicates that Carpenter Technology’s CarTech Puris 5+ titanium powder exceeds standard Ti 6Al-4V Grade 5 strength levels by nearly 18%, providing maximum reusability and high strength. CarTech Puris 5+ titanium powder is a custom composition of Ti 6Al-4V Grade 5 that maintains high strength with lower oxygen content. In 1Q17, Carpenter acquired Puris and its titanium powder assets for $35 million.
Concept Laser and GE Additive are investing in a new 130,000-sq.-ft. 3D printing campus in Lichtenfels, Germany. The ~US $125MM facility will house about 500 employees and open in early 2019. Concept Laser manufactures powder bed-based laser additive manufacturing machines serving aerospace, medical and dental customers. (GE acquired a 75% stake in the company in 4Q16.)
Materialise’s additive manufacturing technology is now integrated into Siemens’ NX™ software, potentially reducing the length of the design-to-manufacturing process by 30% or more. The solution allows NX computer-aided design, manufacturing and engineering software to completely prepare CAD models for powder bed fusion and material jetting 3D printing processes. The integration is notable as it obviates the need for manufacturers to work with separate systems for design and for 3D printing. Data translation issues and lack of associativity between these systems are eliminated.
Sources: Company press releases and websites; images courtesy of manufacturers
Julie A. Vetalice is the Editorial Assistant for ORTHOWORLD.
Call it additive or 3D printing, embrace or eschew it, there is no getting around the reality that the technology is a big deal in orthopaedics.
What follows is by no means a complete representation of all companies that engage this process, but rather a roundup of companies that made headlines within 2017.
Joint Replacement
...
Call it additive or 3D printing, embrace or eschew it, there is no getting around the reality that the technology is a big deal in orthopaedics.
What follows is by no means a complete representation of all companies that engage this process, but rather a roundup of companies that made headlines within 2017.
Joint Replacement
Bodycad received product notification confirmation which enables them to commercially launch their Unicompartmental Knee System within the European Union. Bodycad employs three types of 3D printing technologies—metal, plastic and multi-color modeling/prototyping—to create its implants.
ConforMISÂ received FDA 510(k) clearance of the iTotal Hip replacement system. Limited launch is slated for 2H18. iTotal employs single-use 3D printed instruments.
Corin and Ossis entered a joint venture agreement to develop patient-specific hip and knee implants. The agreement combines Corin’s technologies, such as 3D printing and the Optimized Positioning System, that will complement Ossis’ experience in custom-made implants.
In 1Q17, Lima Corporate celebrated ten years using its proprietary Trabecular Titanium 3D printing technology. (It started with the Delta TT acetabular cup.) In 2Q, the company marked the 15th anniversary of its SMR modular shoulder system by launching SMR bone graft instruments and Lima Personalized Surgical Instruments. At the end of 3Q17, the company announced the milestone of 100,000 implantations of the SMR shoulder system.
Materialise received FDA 510(k) clearance to market its Surgicase Orthopaedics system to assist in pre-op planning for pediatric patients undergoing radius or ulna osteotomy. The system comprises SurgiCase Connect surgical planning software and patient-specific SurgiCase Guides, which are 3D printed.
Medacta received FDA 510(k) clearance and completed first knee revision procedures with 3DMetal Tibial Cones.
Stryker received FDA 510(k) clearance to market the Mako total knee application with Triathlon cementless components; the Tritanium tibial baseplate and metal-backed patella components are built with Stryker’s AMagine additive manufacturing technology. GE Additive and Stryker established an agreement to support Stryker’s growth in additive manufacturing, covering new machines, materials and services.
Spine
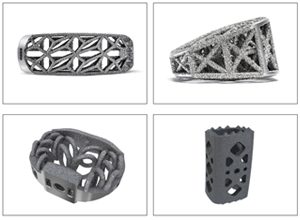
Left to right: 4WEB Medical – Lateral Spine Truss and 3D-printed Anterior Spine Truss Interbody Fusion Systems
Studies indicate that 4WEB Medical’s Lateral Spine Truss demonstrated a better resistance to subsidence vs. an annular interbody implant. The findings indicate the capacity for load distribution inherent to 4WEB’s additively-manufactured truss technology. The company also launched its next-generation 3D-printed Anterior Spine Truss interbody fusion system.
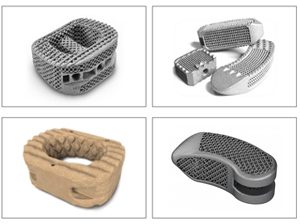
Left to right: ChoiceSpine – HAWKEYE Ti 3D VBR
Camber Spine Technologies – SPIRA Open Matrix ALIF Device
Camber Spine Technologies received FDA 510(k) clearance and commenced U.S. launch of the SPIRA Open Matrix ALIF device, manufactured with additive techniques.
ChoiceSpine received FDA 510(k) clearance to market and announced first clinical use of the HAWKEYE Ti 3D-printed titanium vertebral body replacement, its first 3D-printed device.
Emerging Implant Technologies acquired a portfolio of 22 issued and pending patents covering 3D printed expandable spinal fusion cages, and received FDA 510(k) clearance for 3D-printed spinal interbody devices to address ALIF, PLIF, TLIF and cervical procedures.
HD LifeSciences received FDA 510(k) clearance and commenced U.S. launch of NanoHive, a system of interbody devices for ALIF, PLIF and TLIF procedures. The devices are based on HD’s proprietary, additively-manufactured Soft Titanium™ honeycomb lattice material.
K2M entered into development and supply agreements with 3D Systems that entail an exclusive software solutions partnership and production capacity to support the manufacture of CASCADIA Interbody systems, which feature Lamellar 3D Titanium technology. K2M also acquired exclusive license to a portfolio of 17 patents for expandable interbody fusion devices for development of new products using Lamellar 3D. Finally, the company announced FDA 510(k) clearance of MOJAVE PL, a 3D-printed expandable posterior lumbar interbody system. (3D-printed AND expandable AND FDA-cleared—that was a market first!)
Medicrea received FDA 510(k) clearance to market IB3D 3D-printed interbody devices, and introduced its AdapTEK in-house additive manufacturing technology.
OrthoPediatrics entered into an agreement for exclusive U.S. distribution of Mighty Oak Medical’s FIREFLY pedicle screw navigation guides in pediatric hospitals. FIREFLY guides are 3D-printed, disposable and patient-specific.
Nexxt Spine received FDA 510(k) clearance to market 3D-printed NEXXT MATRIXX interbody and vertebral body replacement devices.
NuVasive unveiled its Advanced Materials Science portfolio, including the 3D-printed titanium Modulus XLIF and porous PEEK technology acquired with its purchase of Vertera Spine.
Renovis Surgical received FDA 510(k) clearance to market Tesera 3D-printed posterior lumbar interbody fusion systems.
RTI Surgical launched the Fortilink-C IBF system, its first device featuring TETRAfuse 3D-printed polymer material.
Stryker Spine received FDA 510(k) clearance and launched its 3D-printed Tritanium C Anterior Cervical Cage.
Trauma
Additive Orthopaedics received FDA 510(k) clearance for its Bunion Correction System and Locking Lattice plate, both constructed via 3D printing. The company also launched a multi-center clinical trial to measure bone in-growth into 3D-printed bone segments.
DePuy Synthes acquired 3D printing technology from Tissue Regeneration Systems to offer patient-specific, bioresorbable implants for orthopaedic and CMF applications.
Supplier News
Arcam will evaluate strategic alternatives regarding its DiSanto Technology contract manufacturing subsidiary (DTI), in efforts to strengthen DTI’s ability to serve as a contract manufacturing partner to orthopaedic customers seeking to combine additive and traditional manufacturing capabilities. Arcam will consider restructuring of DTI, a full or partial separation via a spin-off, sale, joint venture, strategic collaboration or other transaction. (Arcam purchased DTI in 2014 for US $15.8MM; GE purchased Arcam in late 2016.)
ASTM International seeks to establish a center of excellence in additive manufacturing. The entity—an international standards organization that develops and publishes voluntary consensus technical standards for a range of materials, products, systems and services—has called for industry/university proposals aimed at creating a global innovation hub advancing AM technical standards, related R&D, education, training, etc. Further, the center will serve as a consortium in attracting stakeholders from medical and various other industries that are increasingly engaged in AM applications. The winning proposal will be announced in early 2018.
Testing data indicates that Carpenter Technology’s CarTech Puris 5+ titanium powder exceeds standard Ti 6Al-4V Grade 5 strength levels by nearly 18%, providing maximum reusability and high strength. CarTech Puris 5+ titanium powder is a custom composition of Ti 6Al-4V Grade 5 that maintains high strength with lower oxygen content. In 1Q17, Carpenter acquired Puris and its titanium powder assets for $35 million.
Concept Laser and GE Additive are investing in a new 130,000-sq.-ft. 3D printing campus in Lichtenfels, Germany. The ~US $125MM facility will house about 500 employees and open in early 2019. Concept Laser manufactures powder bed-based laser additive manufacturing machines serving aerospace, medical and dental customers. (GE acquired a 75% stake in the company in 4Q16.)
Materialise’s additive manufacturing technology is now integrated into Siemens’ NX™ software, potentially reducing the length of the design-to-manufacturing process by 30% or more. The solution allows NX computer-aided design, manufacturing and engineering software to completely prepare CAD models for powder bed fusion and material jetting 3D printing processes. The integration is notable as it obviates the need for manufacturers to work with separate systems for design and for 3D printing. Data translation issues and lack of associativity between these systems are eliminated.
Sources: Company press releases and websites; images courtesy of manufacturers
Julie A. Vetalice is the Editorial Assistant for ORTHOWORLD.
You are out of free articles for this month
Subscribe as a Guest for $0 and unlock a total of 5 articles per month.
You are out of five articles for this month
Subscribe as an Executive Member for access to unlimited articles, THE ORTHOPAEDIC INDUSTRY ANNUAL REPORT and more.
JV
Julie Vetalice is ORTHOWORLD's Editorial Assistant. She has covered the orthopedic industry for over 20 years, having joined the company in 1999.